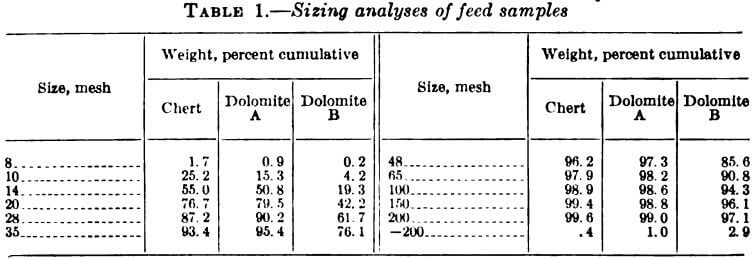
Ball milling is a widely used method for grinding and mixing materials in various industries such as mining, cement, and ceramics. Ball mills come in different shapes and sizes, with different grinding media (balls or rods) and different milling conditions (dry or wet). In this blog, we will discuss the different aspects of ball milling, including ball loads, screens, and flakiness, and compare different types of grinding media.
Ball Rod and Pebble Mills
Ball mills are the most commonly used mills for grinding and mixing materials. They consist of a rotating cylinder filled with balls, rods or pebbles, which are lifted up by centrifugal force and then dropped or shaken to create grinding action. Ball mills can be dry or wet, and can operate in a batch or continuous mode.
Ball Loads
The ball load refers to the total amount of balls, rods or pebbles inside the mill. A higher ball load means more grinding action, but also more energy consumption and wear of the grinding media and mill liners. The optimal ball load depends on the size of the mill and the density and hardness of the material being ground.
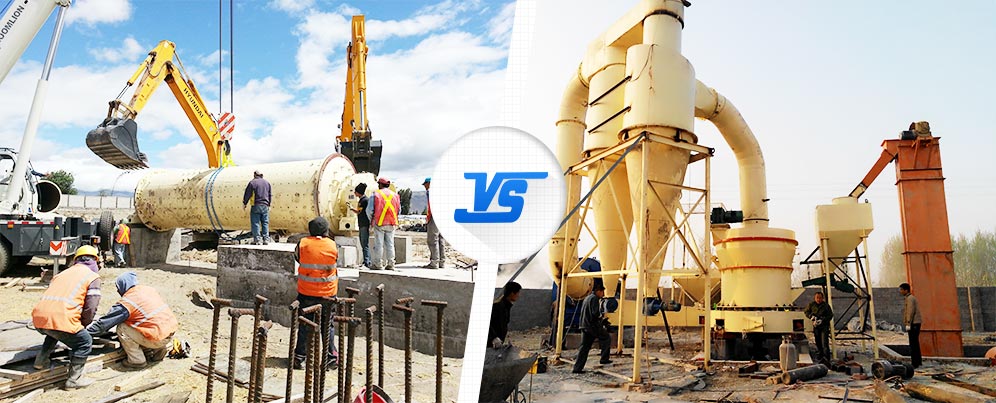
Screens are used in ball milling to control the particle size distribution of the ground material. They are placed at the discharge end of the mill and separate the coarse and fine particles. Flakiness refers to the shape of the particles, and a high flakiness index means that the particle has a high surface area to volume ratio. Flaky particles can cause wear and tear on the mill liners and reduce the grinding efficiency.
Units of Surface
The surface area of the grinding media is an important factor in ball milling. The surface area to volume ratio affects the grinding efficiency, wear rate, and energy consumption. The units of surface can be expressed as either specific surface (area per unit mass) or unit surface (area per unit volume).
Batch and Continuous Grinding Compared
Batch ball milling is used for small-scale grinding and mixing of materials, while continuous ball milling is used for large-scale production. Continuous ball mills require more energy and have higher wear rates than batch mills, but they can produce a higher volume of ground material in a shorter time.
Batch Ball Milling at Various Speeds and Ore Charges
The speed and ball charge of a batch ball mill affect the grinding efficiency and product size distribution. By changing the speed and ball charge, it is possible to optimize the milling conditions to achieve the desired result.
Best Wet and Dry Batch Ball Milling
Wet ball milling is more efficient than dry ball milling because it allows for a larger amount of material to be ground at once. However, dry ball milling can be more cost-effective and easier to operate. The choice between wet and dry ball milling depends on the specific application and preferences of the user.
Selection of Volume of Ball Loads in Continuous Dry Open Circuit Grinding
The volume of ball load in a continuous dry ball mill affects the flow and particle size distribution of the ground material. A higher ball load can lead to overgrinding and finer particles, while a lower ball load can lead to undergrinding and coarser particles.
Nonferrous Media and Steel Balls Compared
Grinding media can be made of different materials, such as steel, ceramic, and nonferrous metals. Steel balls are the most commonly used grinding media in ball milling, but nonferrous media can have advantages such as higher wear resistance and lower contamination.
Sillimanite Balls
Sillimanite balls are made of a high-alumina ceramic material and are used as grinding media in ball milling. They have excellent wear resistance and can be used in both wet and dry milling.
Tetrahedrons and Spherical Balls Compared
Tetrahedral grinding media are becoming increasingly popular in ball milling because of their unique shape and high packing density. They can provide a more efficient grinding and mixing of materials compared to spherical balls.
Battered Reject Balls and New (need remove brand name)
Battered reject balls are grinding media that have become too worn to be effective. They can be recycled and reused as smaller grinding media. New (need remove brand name) are high-quality grinding media designed for maximum wear resistance and efficiency. They are made of a special alloy steel and can be used in both wet and dry ball milling.
In conclusion, ball milling is a versatile and widely used method for grinding and mixing materials in various industries. Understanding the different aspects of ball milling can help optimize the milling conditions and achieve the desired grinding efficiency and product quality. Shanghai VOSTOSUN Industrial Co., Ltd (VOSTOSUN) is a leading manufacturer of ball milling equipment and can provide customized solutions for different applications.