System Introduction
In recent years, with the increasing of environmental resources, the comprehensive utilization of biomass energy has become more and more important to us. Due to the high moisture content of the sawdust, broken wood, which leads the incomplete combustion, resulting in that the spark burns the dust bag at the back of the drying plant, which not only causes the excessive emissions, but also it’s with high cost to change the dust bag. In the process of producing wood products and biomass fuels with high burning combustion value, wood chips and broken dregs are required to do the drying process.
Process Flow
After being fed into the hopper, under the function of gravity the raw material will fall onto the belt conveyor laid under the bottom of the hopper, and then which will be conveyed onto the screening machine, the massive, strip and other irregular material will be separated out after screening, and uniform particles will be conveyed to the feeding end of the dryer (The single cylinder or three cylinder dryer will be chosen as per the service condition) by the belt conveyor under the screening machine. The feeding end of the dryer is connected with heat source and the discharging end is linked with pulse air pipes. The fire wall will be setted up in the hot blast stove in order to guarantee the safety of the drying process, to eliminate the phenomenon of material burning in the dryer, and the heat passing through pipe will be installed between the hot blast stove and the dryer as the section of heat buffer. The material will brought into the diameter-transformed pulse pipe after being dried and the dehydration for the first time inside of the dryer, which will be in a suspended boiling form at the large diameter of the pulse pipe, and then it will be quickly dried after contacting with the exhausted heat wind from dryer. And the material will be driven out of the pulse pipe by strong winds and moved into the first stage cyclone collector when its water content reaches the design requirement, and 80% of dried material will be collected, and then get into the second stage cyclone collector after passing through the induced draft fan to collect the left material. The second stage cyclone collector can be replaced by the bag type dust collector.
System Advantages
Intensive drying strength with short drying time
The light material drying system has advanced design, which let the material has the full contact in the dryer, the full surface area of the particles is the effective drying area, and it has Intensive drying strength. With the pulse air flow dryer, drying time is only half of the regular dryer, the efficiency of the drying machine is greatly increased
Low drying cost with high drying efficiency
The light material drying system has advanced structure, with small mall covered area, easy to construct and to do maintenance. The thermal efficiency can reach 90% when it dries unbound water.
Good drying effect with high level of automation
The final moisture is stable (10%-13%) after the regular light material being dried, and the dried material doesn’t contain impurities. The hot blast stove can be matched with the super temperature alarm, flame monitoring device, tempering alarm, fuel isolation device, which can ensure the safety of combustion.
Technical Parameters
Model | Cylinder diameter(mm) | Cylinder length(mm) | Cylinder volume(m3) | Cylinder rotary speed (r/min) | Power(kW) | Weight(t) |
VS0.6x5.8 | 600 | 5800 | 1.7 | 1-8 | 3 | 2.9 |
VS0.8x8 | 800 | 8000 | 4 | 1-8 | 4 | 3.5 |
VS1x10 | 1000 | 10000 | 7.9 | 1-8 | 5.5 | 6.8 |
VS1.2x5.8 | 1200 | 5800 | 6.8 | 1-6 | 5.5 | 6.7 |
VS1.2x8 | 1200 | 8000 | 9 | 1-6 | 5.5 | 8.5 |
VS1.2x10 | 1200 | 10000 | 11 | 1-6 | 7.5 | 10.7 |
VS1.2x11.8 | 1200 | 11800 | 13 | 1-6 | 7.5 | 12.3 |
VS1.5x8 | 1500 | 8000 | 14 | 1-5 | 11 | 14.8 |
VS1.5x10 | 1500 | 10000 | 17.7 | 1-5 | 11 | 16 |
VS1.5x11.8 | 1500 | 11800 | 21 | 1-5 | 15 | 17.5 |
VS1.5x15 | 1500 | 15000 | 26.5 | 1-5 | 15 | 19.2 |
VS1.8x10 | 1800 | 10000 | 25.5 | 1-5 | 15 | 18.1 |
VS1.8x11.8 | 1800 | 11800 | 30 | 1-5 | 18.5 | 20.7 |
VS1.8x15 | 1800 | 15000 | 38 | 1-5 | 18.5 | 26.3 |
VS1.8x18 | 1800 | 18000 | 45.8 | 1-5 | 22 | 31.2 |
VS2x11.8 | 2000 | 11800 | 37 | 1-4 | 18.5 | 28.2 |
VS2x15 | 2000 | 15000 | 47 | 1-4 | 22 | 33.2 |
VS2x18 | 2000 | 18000 | 56.5 | 1-4 | 22 | 39.7 |
VS2x20 | 2000 | 20000 | 62.8 | 1-4 | 22 | 44.9 |
VS2.2x11.8 | 2200 | 11800 | 44.8 | 1-4 | 22 | 30.5 |
VS2.2x15 | 2200 | 15000 | 53 | 1-4 | 30 | 36.2 |
VS2.2x18 | 2200 | 18000 | 68 | 1-4 | 30 | 43.3 |
VS2.2x20 | 2200 | 20000 | 76 | 1-4 | 30 | 48.8 |
VS2.4x15 | 2400 | 15000 | 68 | 1-4 | 30 | 43.7 |
VS2.4x18 | 2400 | 18000 | 81 | 1-4 | 37 | 53 |
VS2.4x20 | 2400 | 20000 | 91 | 1-4 | 37 | 60.5 |
VS2.4x23.6 | 2400 | 23600 | 109 | 1-4 | 45 | 69.8 |
VS2.8x18 | 2800 | 18000 | 111 | 1-3 | 45 | 62 |
VS2.8x20 | 2800 | 20000 | 123 | 1-3 | 55 | 65 |
VS2.8x23.6 | 2800 | 23600 | 148 | 1-3 | 55 | 70 |
VS2.8x28 | 2800 | 28000 | 172 | 1-3 | 75 | 75 |
VS3x20 | 3000 | 20000 | 141 | 1-3 | 55 | 75 |
VS3x23.6 | 3000 | 23600 | 170 | 1-3 | 75 | 85 |
VS3x28 | 3000 | 28000 | 198 | 1-3 | 90 | 91 |
VS3.2x23.6 | 3200 | 23600 | 193 | 1-3 | 90 | 112 |
VS3.2x32 | 3200 | 32000 | 257 | 1-3 | 110 | 129 |
VS3.6x36 | 3600 | 36000 | 366 | 1-3 | 132 | 164 |
VS3.8x36 | 3800 | 36000 | 408 | 1-3 | 160 | 187 |
VS4x36 | 4000 | 36000 | 452 | 1-3 | 160 | 195 |
Working Sites’ Pics
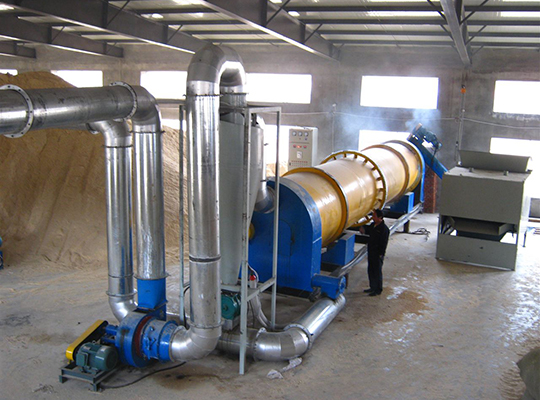
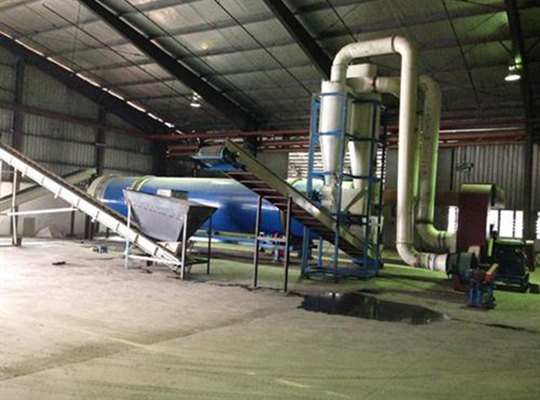