Operating Principle
This equipment adopts the fixed vacuum chamber, the rubber belt is driven by the gearbox and running continuously on the vacuum chamber, the cloth moving synchronously on the rubber belt. The friction belt on the slipway of vacuum chamber forming a water sealing structure with rubber belt. The slurry feeding on the cloth smoothly and evenly by feeding hopper. When the vacuum chamber connects with vacuum system, the filtering area with vacuum suction will be formed on the rubber belt, the filtrate pass through the cloth and flow to the grooves and holes of rubber belt to vacuum chamber, the solids formed a cake on the surface of cloth. The filtrate in the vacuum chamber discharged by the vacuum tank. Moving by the rubber belt, the cake moving to the cake washing area and drying area sequentially, then enter into cake discharging area. After discharging cake, the cloth washed by washing system and enter into next filtering cycle.Features
● Modular design, flexible assembly and convenient transportation are implemented for structure. Also, can deliver the whole assembled equipment after assembly and test running. ● The filter cloth and rubber belt operating synchronously is applied to the filter, which can be finished the process of continuous feeding, filtering, washing, drying and cloth washing. ● The remote control and local control can be exchanged to achieve unmanned operations. ● On the rubber belt support, we can use rollers, air cushion, pallet and multiple friction belts to reduce the friction resistance and prolong the rubber belt life time. ● Use filtrate or clean water for the cake washing, and collect the filtrate by sections. ● Use high pressure water for cloth washing to increase the cloth regenerative effect and the life span. ● Filtrate discharge types include automatic discharge, high level discharge and auxiliary discharge. ● Gas cover or aluminum plastic windows can be designed partial closed or totally enclosed for partial insulation or the centralized collection for the volatile gas or steam of slurry.Technical Specification
Filtrating area (M2) | Effective width (mm) | Effective length (mm) | Frame length (mm) | Frame width (mm | Frame height (mm) | Weight (T) | Vacuum consumption (m3/min) |
2 | 500 | 4000 | 8100 | 1100 | 2070 | 5.5 | 8 |
3 | 6000 | 10100 | 6 | 12 | |||
4 | 8000 | 12100 | 6.5 | 16 | |||
5 | 10000 | 14100 | 7 | 18 | |||
6 | 12000 | 16100 | 7.6 | 22 | |||
8 | 1000 | 8000 | 12100 | 1600 | 2070 | 8.8 | 25 |
10 | 10000 | 14100 | 9.6 | 28 | |||
12 | 12000 | 16100 | 10.4 | 30 | |||
14 | 14000 | 18100 | 11.1 | 33 | |||
10.4 | 1300 | 8000 | 12100 | 1900 | 2170 | 9.8 | 28 |
13 | 10000 | 14100 | 10.8 | 30 | |||
15.6 | 12000 | 16100 | 11.5 | 35 | |||
18.2 | 14000 | 18100 | 13.2 | 38 | |||
20.8 | 16000 | 20100 | 15.1 | 42 | |||
20 | 2000 | 10000 | 14100 | 2700 | 2170 | 14.2 | 40 |
24 | 12000 | 16100 | 17.8 | 48 | |||
28 | 14000 | 18100 | 20.2 | 52 | |||
32 | 16000 | 20100 | 23.6 | 65 | |||
20 | 2500 | 8000 | 12100 | 3200 | 2270 | 14.8 | 40 |
25 | 10000 | 14100 | 18.6 | 50 | |||
30 | 12000 | 16100 | 22.2 | 60 | |||
35 | 14000 | 18100 | 26 | 70 | |||
40 | 16000 | 20100 | 29.8 | 80 | |||
50 | 20000 | 24100 | 41 | 95 | |||
30 | 3000 | 10000 | 14100 | 3750 | 2270 | 22.8 | 60 |
36 | 12000 | 16100 | 27.5 | 72 | |||
42 | 14000 | 18100 | 32.5 | 85 | |||
54 | 18000 | 22100 | 45 | 105 | |||
60 | 20000 | 24100 | 50.5 | 120 | |||
48 | 4000 | 12000 | 16100 | 4800 | 2470 | 39.5 | 92 |
56 | 14000 | 18100 | 46.8 | 110 | |||
64 | 16000 | 20100 | 52.6 | 120 | |||
72 | 18000 | 22100 | 58.3 | 145 | |||
80 | 20000 | 24100 | 63 | 160 | |||
144 | 4500 | 32500 | 41200 | 7100 | 5500 | 70 | 360 |
Process Flow Diagram
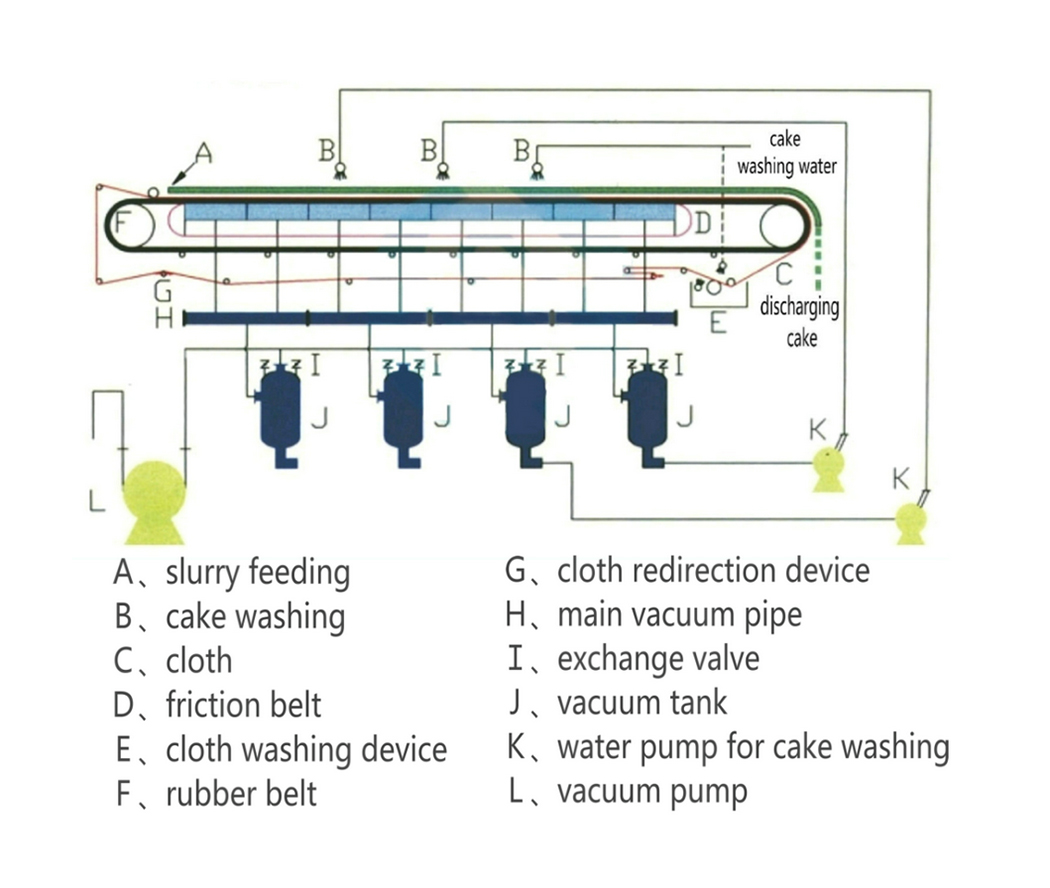
Main Parts
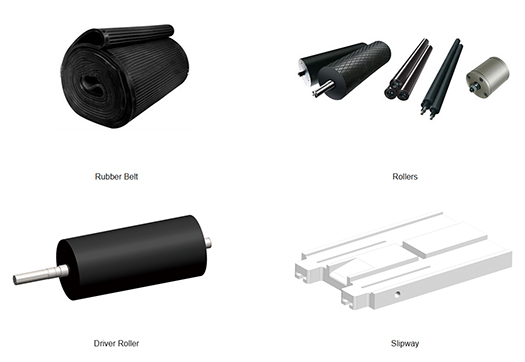
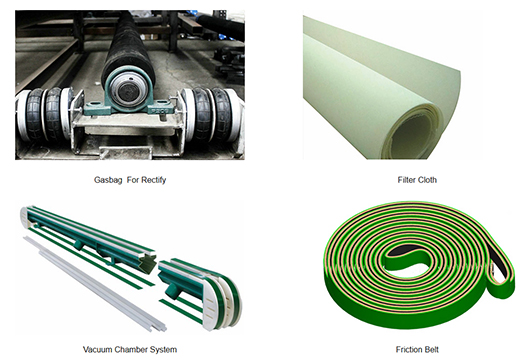
Working sites’ Pics
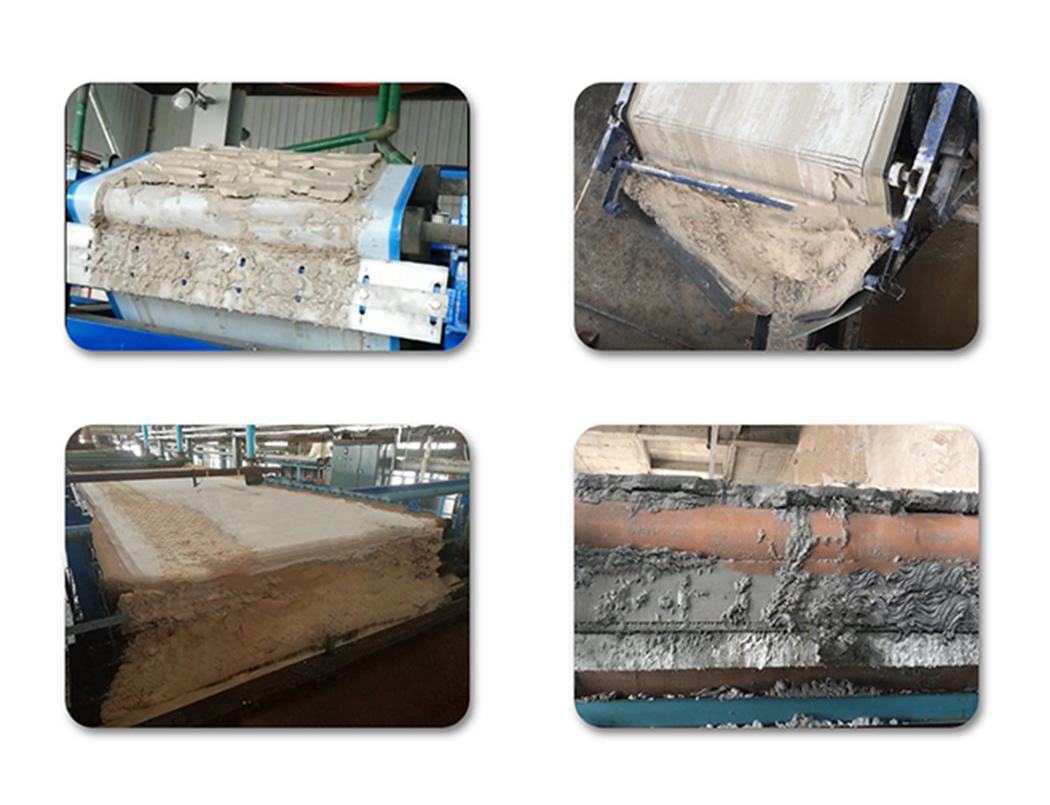